The Future of Business: Excelling in Design for Additive Manufacturing
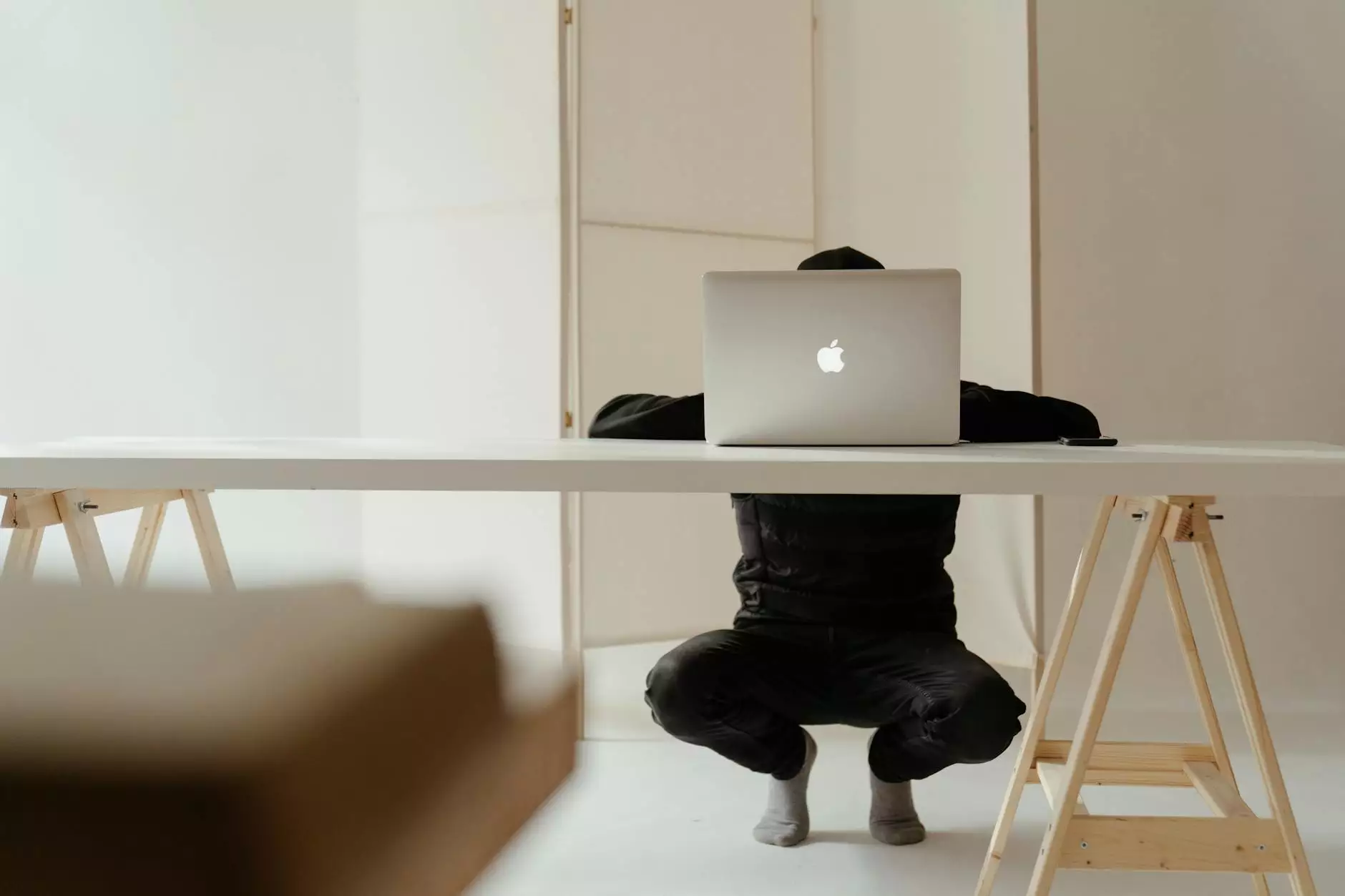
In today's rapidly evolving technological landscape, the importance of design for additive manufacturing (DFAM) has emerged as a cornerstone for businesses seeking to thrive. As industries increasingly adopt 3D printing technologies, the implications for product design, cost efficiency, and sustainability are profound. This article delves into the intricate relationship between DFAM and modern business practices, exploring its benefits and offering insights into how companies like arti90.com are harnessing this innovative approach.
Understanding Design for Additive Manufacturing
Design for additive manufacturing refers to a set of design principles that optimize products for the unique capabilities and processes associated with additive manufacturing, particularly 3D printing. Unlike traditional subtractive manufacturing methods, where materials are cut away from a solid block, additive manufacturing builds products layer by layer. This fundamental shift opens up new avenues for creativity and efficiency in product development.
Key Concepts in DFAM
- Material Efficiency: Utilizing materials more effectively reduces waste and lowers costs.
- Complex Geometry: Enables intricate shapes that were previously unattainable with traditional methods.
- Customization: Facilitates personalized products for specific customer requirements.
- Rapid Prototyping: Accelerates the development process, allowing for quicker iterations and feedback.
- Supply Chain Optimization: Streamlines production and logistics by reducing the number of parts needed.
The Business Advantages of Implementing DFAM
Businesses that embrace design for additive manufacturing are positioned to gain a competitive edge in several critical areas:
1. Cost Reduction
By minimizing material waste and streamlining production processes, companies can significantly reduce manufacturing costs. DFAM strategies enable businesses to create parts that require less raw material and eliminate the need for extensive tooling, leading to substantial savings.
2. Enhanced Productivity
With 3D printing, production times can be drastically reduced. Rapid prototyping allows for testing and validation phases to occur much faster than traditional manufacturing methods. This efficiency not only accelerates time-to-market but also enables businesses to respond swiftly to market demands.
3. Innovation and Flexibility
Adopting DFAM encourages a culture of innovation. Designers and engineers can experiment with complex geometries, which previously could not be manufactured at scale. This freedom fosters creativity in developing unique product solutions tailored to consumer needs.
4. Sustainability
In an age where environmental concerns are paramount, DFAM promotes sustainable practices by significantly reducing material waste and energy consumption. Companies focused on sustainability gain customer loyalty and bolster their brand image in an increasingly eco-conscious market.
5. Customization and Personalization
Personalized products resonate more with consumers than mass-produced items. DFAM allows businesses to quickly adapt their designs to meet individual customer specifications, whether it’s a custom fit, design, or function, leading to higher customer satisfaction and engagement.
Case Studies: Businesses Leveraging DFAM
Many companies worldwide have successfully integrated design for additive manufacturing into their business models, showcasing the versatility and potential of this approach.
Case Study 1: Arti90’s Innovative Approach
As a leader in Art Supplies and Product Design, arti90.com has embraced DFAM to enhance its offerings. By utilizing 3D printing, the company has been able to produce bespoke art tools that cater specifically to the unique needs of their artist clientele. This innovation not only differentiates their products from competitors but also fosters a strong connection with their customers.
Case Study 2: Aerospace Industry Transformation
In the aerospace sector, companies like Boeing and Airbus are utilizing DFAM to create lighter components, thereby improving fuel efficiency and reducing emissions. Through advanced 3D printing techniques, they are able to manufacture parts that are both incredibly strong and lightweight, revolutionizing air travel.
Steps to Implement DFAM in Your Business
If you’re considering integrating design for additive manufacturing into your business strategy, here are some essential steps to guide you:
1. Educate Your Team
Understanding the principles and practices of DFAM is crucial. Offer training sessions and workshops to ensure that your design and engineering teams are well-versed in the capabilities and limitations of 3D printing.
2. Invest in the Right Technology
Select the appropriate 3D printing technologies and materials that align with your business goals. With multiple options available, choosing the right equipment is essential for maximizing the benefits of DFAM.
3. Emphasize Collaboration
Foster a culture of collaboration within your organization. Involve teams from design, engineering, and production to ensure that everyone is aligned in the application of DFAM principles.
4. Prototype and Iterate
Use rapid prototyping to develop and refine product designs. The ability to quickly test and iterate on designs helps in achieving optimal results while minimizing costs.
5. Monitor and Adjust
After implementing DFAM, continuously monitor its impact on your business processes. Gather feedback from your team and customers to make necessary adjustments and improvements.
The Future of DFAM in Business
The trends indicate that design for additive manufacturing will continue to reshape industries as technology advances. As 3D printing capabilities expand, businesses that adapt to these changes will remain competitive. For example, future advancements in materials science could open doors for new applications we have yet to imagine.
Emerging Technologies
Technologies like artificial intelligence and machine learning are also starting to play a significant role in DFAM. These technologies can assist in designing components with optimal performance and durability, making the DFAM process even more effective.
Industry Adoption Trends
As industries from healthcare to automotive adopt additive manufacturing, the demand for skilled professionals who understand DFAM will grow. This demand presents a valuable opportunity for educational institutions and training programs to prepare the workforce of tomorrow.
Conclusion
Embracing design for additive manufacturing represents not just a trend, but an essential shift in how businesses approach product design and manufacturing. The advantages of cost reduction, enhanced innovation, and improved sustainability cannot be overstated. As companies like arti90.com have demonstrated, the integration of DFAM can lead to significant competitive advantages, positioning businesses for future success.
By prioritizing DFAM, companies can not only meet current market demands but also pave the way for innovative solutions that will define the future of their industries. Now is the time to explore how your business can harness the power of additive manufacturing to drive growth and success.