Unveiling the World of Precision Plastic Molding
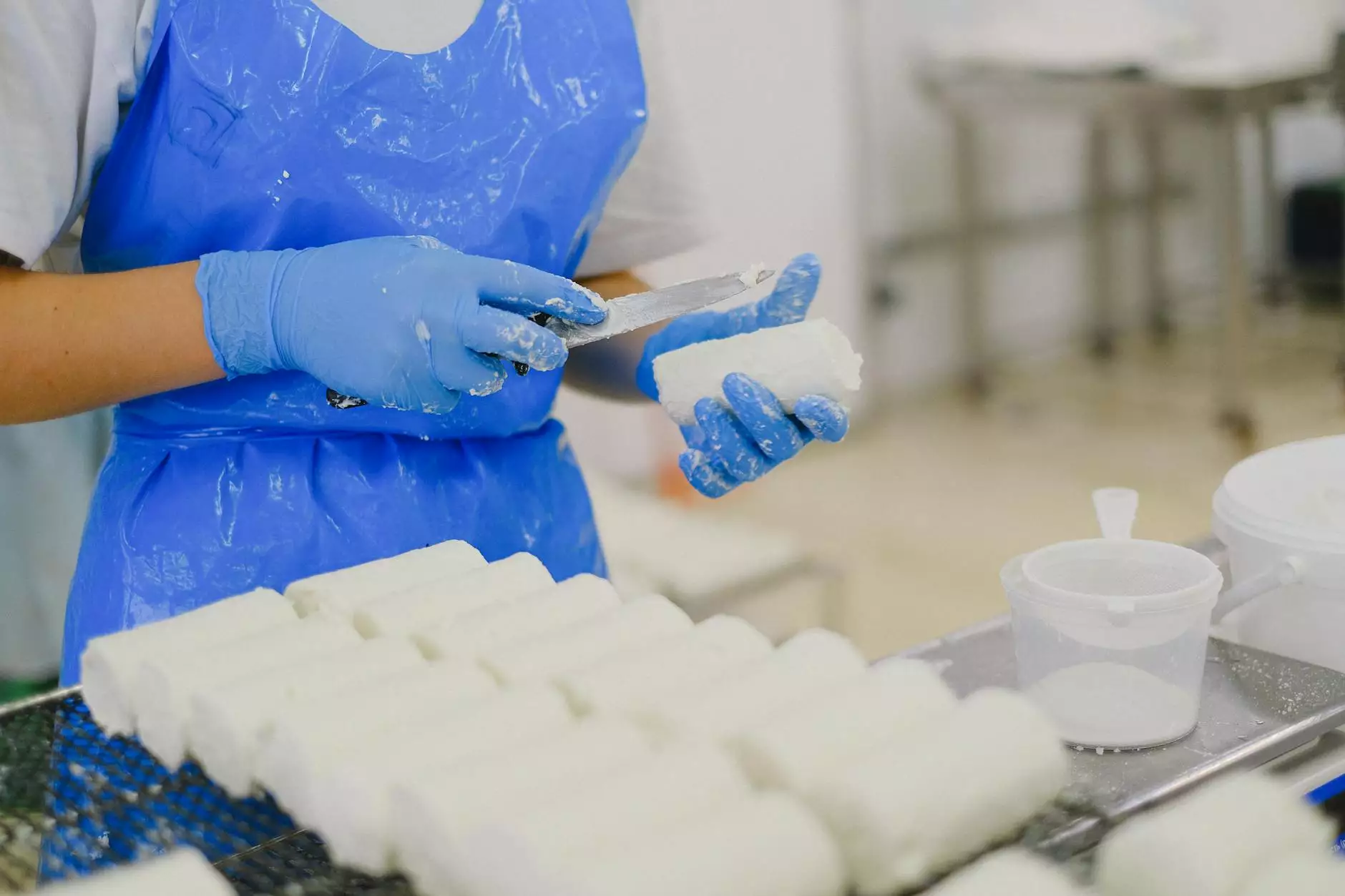
Precision plastic molding is transforming manufacturing paradigms, particularly for businesses operating in the metal fabrication sector. As industries evolve, the demand for parts that are not only durable but also lightweight has surged, making precision plastic molding an invaluable tool for metal fabricators. In this article, we will delve into the intricacies of precision plastic molding, exploring its processes, benefits, applications, and how it complements traditional metal fabrication techniques.
The Fundamentals of Precision Plastic Molding
At its core, precision plastic molding is a manufacturing process used to create intricate plastic parts with high accuracy and detail. This method involves injecting molten plastic into a mold cavity, where it cools and solidifies, resulting in a finished component. The precision aspect is vital, as it ensures that the final product adheres to strict specifications and tolerances.
Key Steps in the Precision Plastic Molding Process
- Mold Design: The foundation of precision plastic molding begins with sending information regarding part design to specialists who create molds tailored to the specific requirements.
- Material Selection: A variety of thermoplastic materials can be used, such as ABS, Polycarbonate, and Nylon, each having unique properties suited to different applications.
- Injection Process: The heated plastic material is injected into the mold at high pressure, allowing it to fill every nook and cranny, ensuring no defects occur.
- Cooling and Ejection: After the material cools and solidifies, the mold opens to eject the finished part, ready for inspection and assembly.
Why Choose Precision Plastic Molding?
The advantages of precision plastic molding extend beyond just creating parts; they are varied and significant for businesses in the metal fabrication domain.
Benefits of Precision Plastic Molding
- High Tolerance Levels: Hitting precise measurements with minimal deviation is fundamental for component functionality, and precision plastic molding excels in this regard.
- Cost-Effectiveness: When in high-production volumes, the cost of plastic parts produced through this method is generally lower than many traditional methods, including machining.
- Design Flexibility: Designers can push the limits of creativity, as molds can be constructed in virtually any shape, enabling complex designs that are unachievable through other means.
- Reduced Weight: Plastic components typically weigh less than their metal counterparts, which can lead to lower shipping costs and enhanced energy efficiency in the end-use application.
- Environmentally Friendly Options: Many plastics used in precision molding can be recycled, and advancements in bioplastics provide greener alternatives.
Applications Across Sectors
The applications of precision plastic molding are extensive and vary across numerous industries. Here are some noteworthy domains where these techniques are pivotal:
1. Automotive Industry
Automakers utilize precision plastic molding for creating exterior and interior components. Lightweight plastic parts not only contribute to fuel efficiency but also provide design flexibility for highly technical shapes required in modern vehicles.
2. Medical Sector
In the medical field, the precision of molded parts is crucial. Devices such as syringes, surgical instruments, and diagnostic equipment require high standards of accuracy, which precision plastic molding can reliably provide.
3. Electronics Manufacturing
Electronics housing often incorporates precision plastic molded parts. These components not only protect delicate internal circuitry but also enhance aesthetic appeal. Molding allows for intricate designs, including features for improved ergonomics.
4. Consumer Goods
From toys to household appliances, consumer goods manufacturers turn to precision plastic molding for effective, scalable production of visually appealing and functional products.
Integrating Precision Plastic Molding in Metal Fabrication
As the landscape of manufacturing shifts, metal fabricators increasingly embrace precision plastic molding as a complement to traditional methods. This integration offers several compelling synergies:
1. Enhanced Product Performance
By incorporating plastic components, metal fabricators can enhance the overall functionality of their products, taking advantage of plastics' non-corrosive properties, lightweight nature, and design versatility.
2. Streamlined Production Processes
Combining metal and plastic strategies paves the way for more efficient assembly lines, reducing labor costs and final product lead times.
3. Innovation in Product Design
The ability to meld plastics with metals accelerates innovative product designs that could result in new market trends and opportunities.
Quality Control in Precision Plastic Molding
Quality assurance is paramount in precision plastic molding processes. Implementing robust quality control measures helps ensure that every part produced meets stringent specifications.
Key Quality Control Practices
- Regular Inspection: Conducting routine inspections during the molding process can catch discrepancies early, saving time and costs associated with rework.
- Material Testing: Before production, all raw materials should be tested for consistency to guarantee the integrity of the final product.
- Final Product Testing: After production, parts should undergo stringent testing to ensure they meet final specifications and performance standards.
Conclusion
In summary, precision plastic molding is more than just a manufacturing process; it represents a pivotal shift in how modern manufacturing integrates and optimizes traditional and innovative techniques. For metal fabricators seeking to enhance their capabilities, understanding and leveraging precision plastic molding offers a pathway to greater efficiency, improved product performance, and sustained competitive advantage.
By incorporating precision plastic molding into their operations, metal fabricators can stay ahead in an ever-evolving market, ensuring not only the survival of their business but also its growth and leadership in the industry. Embrace the future of manufacturing and explore the vast opportunities presenting themselves through precision plastic molding.
For more information on how your business can benefit from precision plastic molding, visit DeepMould.net.