Silicone Rubber Sheet for Vacuum Press: Unlocking Versatility and Efficiency
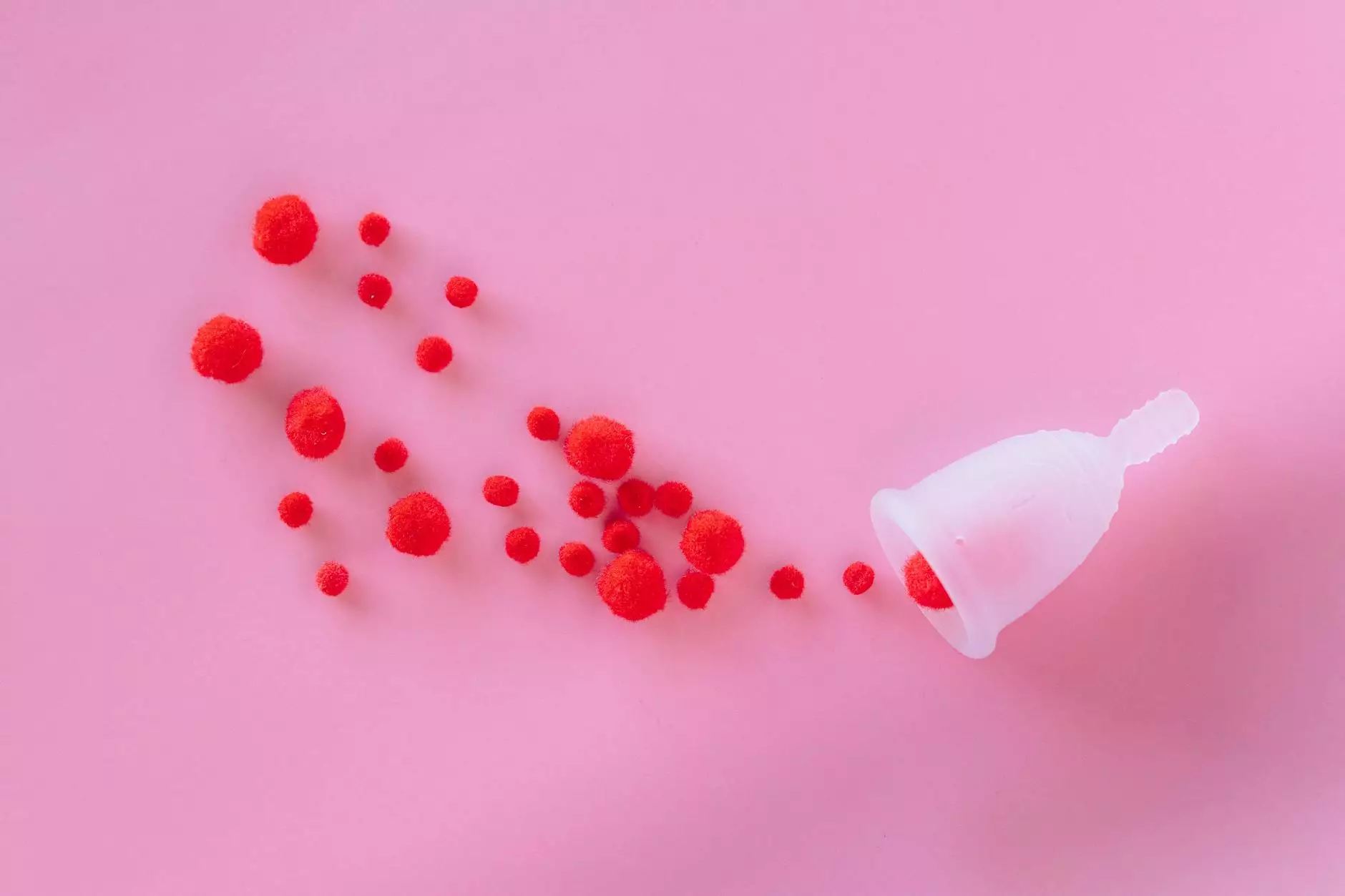
Silicone rubber sheets have become a cornerstone in various industries, particularly for vacuum press applications. With their extraordinary properties and wide-ranging usability, these sheets are instrumental in the Health & Medical, Beauty & Spas, and Medical Spas sectors. This article delves into the intricate details of silicone rubber sheets for vacuum presses, outlining their benefits, applications, and why they are essential tools for professionals.
The Unique Properties of Silicone Rubber
Silicone rubber is known for its remarkable features that set it apart from other materials. These include:
- High Temperature Resistance: Silicone rubber can withstand extreme temperatures, maintaining its integrity and performance in both high and low settings.
- Excellent Flexibility: Its flexibility ensures that it can conform to various shapes and surfaces, making it perfect for vacuum applications.
- Non-stick Surface: Silicone has natural non-stick properties, which are beneficial when working with adhesives, resins, and other materials.
- Chemical Resistance: Silicone rubber is resistant to a wide range of chemicals, making it suitable for demanding environments.
- Durability: The longevity of silicone rubber sheets means less frequent replacements, contributing to long-term cost efficiencies.
What is a Vacuum Press?
A vacuum press is a device that applies pressure to a material by evacuating air from inside a chamber. This process creates a vacuum that pulls the materials together, ensuring a tight bond without air pockets. It is widely used in various industries for applications such as:
- Woodworking: Laminating wood layers for furniture pieces.
- Composites: Fusing layers of composite materials in automotive and aerospace manufacturing.
- Medical Applications: Assisting in creating molds for medical devices and prosthetics.
Why Choose Silicone Rubber Sheets for Vacuum Press?
The key to successful vacuum pressing lies in the materials used. Silicone rubber sheets are particularly advantageous for several reasons:
1. Perfect Sealing Capabilities
Silicone rubber ensures that the vacuum press maintains an optimal seal, preventing air leaks, which is crucial for effective pressure application and material bonding.
2. Temperature Tolerance
During the vacuum pressing process, materials often experience varying temperatures. Silicone rubber sheets can withstand these shifts without losing performance, ensuring consistent results.
3. Easy Maintenance
Silicone is easy to clean and maintain, reducing downtime between uses. Its non-porous surface ensures that residues from previous applications do not affect subsequent jobs.
4. Compatibility with Various Materials
Silicone rubber sheets are compatible with multiple substrates, including resins, plastics, and metals, making them a versatile choice for professionals.
Applications in Health & Medical
In the Health & Medical sector, silicone rubber sheets are essential. They play a vital role in creating prototypes, molds, and medical devices like:
- Prosthetic limbs and components.
- Medical trays and sterilization packaging.
- Support in orthopedic applications for custom molding.
Using silicone rubber sheets enhances the precision of these applications, ensuring that the final products meet the stringent quality requirements typical of the medical industry.
Applications in Beauty & Spas
In the Beauty & Spa industries, these sheets find use in:
- Facial mask applications where molding and adherence to skin are critical.
- Producing tools for aesthetic treatments, ensuring safety and efficacy.
- Creating custom molds for spa equipment that improves functionality and user experience.
By utilizing silicone rubber sheets for vacuum pressing, beauty professionals can achieve higher quality and precision in their products, resulting in better customer satisfaction and overall efficiency.
Applications in Medical Spas
Medical spas benefit immensely from silicone rubber sheets in various ways:
- Custom-molded equipment that fits individual patient needs.
- Creation of specialized treatment tools that require airtight seals during application.
- Enhanced safety during procedures due to the non-toxic and flexible nature of silicone.
This adaptability makes silicone rubber sheets indispensable in medical spas, where patient satisfaction and safety are paramount.
How to Choose the Right Silicone Rubber Sheet
When selecting a silicone rubber sheet for vacuum press applications, consider the following factors:
- Thickness: Choose based on the specific requirements of your application. Thicker sheets provide more durability but may be less flexible.
- Durometer: Hardness is essential to meet the application’s needs. Softer sheets can mold better, while harder sheets provide strength.
- Temperature Rating: Ensure the sheet can handle the temperature ranges encountered during your processes.
- Size: Ensure the sheet is available in sizes that meet the dimensions of your vacuum press to avoid cutting or additional waste.
Conclusion: Enhancing Efficiency with Silicone Rubber Sheets
In conclusion, the utilization of silicone rubber sheets for vacuum press applications brings about substantial benefits across various sectors, including Health & Medical, Beauty & Spas, and Medical Spas. Their unique properties, such as high temperature resistance, flexibility, and compatibility with different materials, make them the go-to choice for professionals aiming for efficiency and quality in their work. By understanding their applications and advantages, businesses can leverage silicone rubber sheets to enhance productivity and ensure customer satisfaction.
For those looking to invest in silicone rubber sheets, platforms like silicone-membranes.eu offer a range of products designed to meet varied needs. Explore the advantages today and discover how silicone can revolutionize your processes!