The Comprehensive Guide to Die Casting Machine Parts
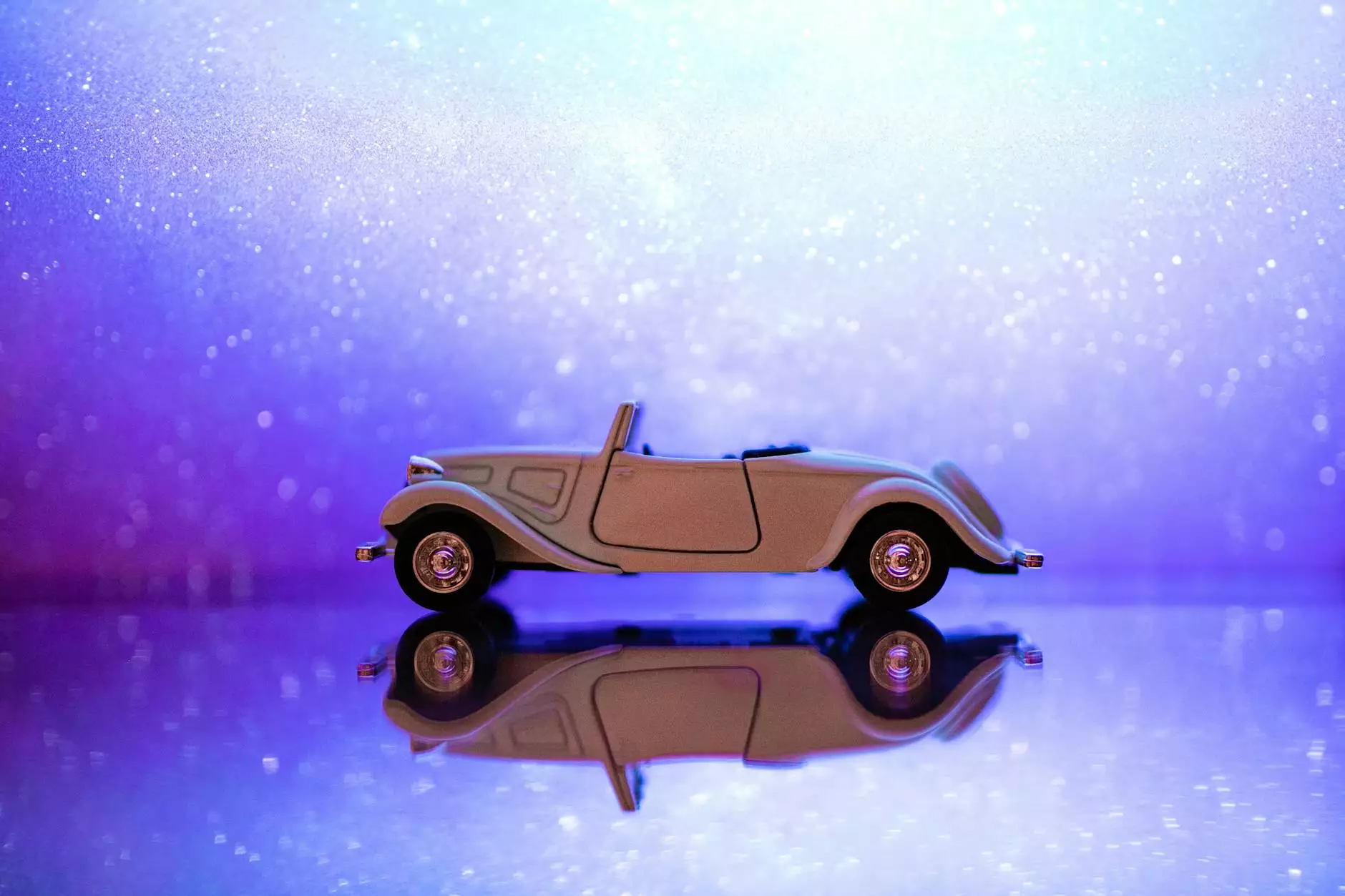
In the ever-evolving world of manufacturing, die casting machine parts play a pivotal role. As industries strive for greater efficiency, the demand for high-quality metal components has surged. This article delves into the significance, manufacturing processes, and essential components related to die casting, providing valuable insights for professionals looking to enhance their understanding of this crucial domain.
Understanding Die Casting
Die casting is a manufacturing process where molten metal is injected into a mold cavity, creating precise and complex shapes. It is renowned for producing high-strength components in various sizes. The method typically employs metals such as aluminum, zinc, and magnesium, allowing manufacturers to create intricate parts with excellent surface finishes.
Importance of Die Casting Machine Parts
Die casting machine parts are integral to the success of the die casting process. Understanding their role can significantly impact production quality and efficiency:
- Precision: Die casting provides high dimensional accuracy, which is critical for parts that must fit together seamlessly in assemblies.
- Strength: The metal components produced through this process tend to have superior mechanical properties, making them suitable for high-stress applications.
- Complex Geometries: Die casting allows for the production of intricate shapes that are often impossible or cost-ineffective to create using other methods.
- Low Waste: The process minimizes material waste, thereby making it an environmentally friendly option among manufacturing techniques.
Key Components of Die Casting Machines
To fully appreciate the significance of die casting machine parts, one must familiarize themselves with the key components that make up these machines. Each part has a specific function that contributes to the overall efficiency and effectiveness of the die casting process:
1. Die
The die is the heart of the die casting machine. It consists of two halves: the stationary die and the ejector die. The design of the die determines the shape and features of the finished part. High-quality dies can withstand the extreme pressure and temperature of molten metal, ensuring durability and accuracy.
2. Injection System
The injection system is responsible for delivering molten metal into the die. This system includes the injection unit, which heats and injects the metal at high pressure. The precision of this system greatly influences the quality of the cast parts.
3. Clamping Unit
The clamping unit holds the die in place during the injection process. It must be capable of applying significant force to keep the die closed under the immense pressure of the injected metal. An inadequate clamping unit can lead to defects in the casting.
4. Cooling System
Cooling systems are integral for regulating the temperature of the die to optimize the casting cycle time. Efficient cooling not only helps in maintaining the shape of the part but also enhances the overall lifespan of the die.
5. Ejection System
Once the metal has solidified, the ejection system facilitates the removal of the cast part from the die. It must operate smoothly to avoid damaging the finished product, ensuring a quick turnover for subsequent cycles.
The Die Casting Process Explained
The process of die casting involves several critical steps that ensure the creation of high-quality parts. Here’s a detailed overview:
1. Mold Preparation
Before any casting can take place, the molds are prepared by applying a release agent to prevent the metal from sticking. The accuracy of the molds is vital as they dictate the final dimensions of the parts.
2. Melting the Metal
Next, the selected metal alloy is melted in a furnace. The metal must reach the appropriate temperature to facilitate easy flow into the mold without compromising its properties.
3. Injection of Molten Metal
Once the metal is melted, it is injected into the mold cavity under high pressure. This step is crucial for filling the mold completely and ensuring that no air pockets remain that could weaken the part.
4. Cooling and Solidification
After the mold is filled, the molten metal is allowed to cool and solidify. The cooling time depends on the size and complexity of the part being cast.
5. Ejection of the Casting
Once solidified, the clamping unit releases the die, and the ejection system removes the finished part. This step must be performed delicately to prevent damage.
6. Finishing Operations
Finally, the cast part may undergo additional finishing operations such as machining, surface treatment, or inspection to meet quality standards.
Applications of Die Casting
Die-cast parts are utilized across various industries due to their exceptional properties. Here are some key applications:
- Automotive Industry: From engine parts to chassis components, the automotive industry heavily relies on die casting for lightweight yet durable components.
- Aerospace Industry: Die casting is used for manufacturing intricate components that require precision and strength, contributing to the overall safety and efficiency of aircraft.
- Consumer Electronics: The electronics sector benefits from die casting for producing enclosures, heat sinks, and components that require high thermal conductivity.
- Medical Devices: Quality and precision are paramount in medical devices, making die casting a favorable choice for various parts and assemblies.
The Future of Die Casting
The future of die casting is bright, with advancements in technology enhancing production capabilities. Key trends include:
- 3D Printing Integration: The integration of 3D printing with die casting may revolutionize mold production and design, allowing for more complex geometries and faster prototyping.
- Sustainable Practices: As industries aim for greener practices, die casting manufacturers are exploring sustainable materials and recycling techniques to minimize waste.
- Smart Manufacturing: Automation and IoT technologies are set to optimize die casting processes further, improving efficiency, monitoring, and maintaining quality standards.
Conclusion
In conclusion, die casting machine parts are vital for the manufacturing industry, delivering precision, strength, and efficiency. The processes and components discussed in this article underscore the intricacies involved in die casting and illuminate the many applications that benefit from this method. As the industry evolves, adapting to new technologies and sustainable practices will be key to maintaining competitive advantages in an increasingly complex market.
To learn more about die casting and its associated parts, visit deepmould.net, your reliable source for metal fabrication solutions.